Control optimisation of sand traps in wastewater treatment plants with Katronic‘s fixed flow measuring system
Ultrasonic flowmeter operates as turbidity and flow monitor for grit trap control at wastewater treatment plants, reducing pump and scraper operation by up to 85%
In classic three-stage wastewater treatment plants, grit and grease traps are indispensable as a process step in the first mechanical pre-treatment stage, as all substances that can lead to operational disturbances (wear, clogging) within the plant are filtered here. Sand, stones, glass, mineral solids and other impurities with grain sizes of 0.2 mm to 1 mm settle to the bottom of the grit chamber. In modern plants, the grit is washed after removal from the grit chamber in order to achieve better dewatering and reusability of the mineral solids (for example in road construction). Then, in a second step, the wastewater is pre-clarified (sedimentation) before being passed on for further treatment.
Technisches Büro Holger Pinta uses Katronic’s fixed ultrasonic flow measurement systems to detect turbidity due to sand build-up in sand trap pressure lines, and uses the measurement to control pumping processes more efficiently.
The clamp-on transducers of the permanently installed flow measurement units - which are usually used for flow measurements of liquids with low solids content - detect turbidity due to sand as an expression of reduced signal strength as the sand in the line scatters the ultrasonic pulse. The measurement and experience values gained over the years, as well as modelling, make it possible today to evaluate the turbidity generated by sand in the pressure line in such a way that reductions in operating times of the sand trap pump and scraper of up to 85 % can be achieved. Another advantage of this application is to be able to continuously monitor the pump delivery rate. Users who know their process peaks better can better control the energy input for their grit trap pumps and thus counteract early, high wear.
Two special ultrasonic sensors detect the turbidity without contact with the medium in the sand trap pressure line designed between DN 80 ... DN 100 mm after the floating sludge pump is switched on. The two transducers (transmitter + receiver) are attached by means of special pipe clamps on the outside of a vertical section of the pressure pipe. They are hard-wired to the Katronic transmitter and a 4-20mA signal proportional to turbidity is supplied to the central control system.
In addition, the weather situation is included via a humidity and air pressure sensor. In a control system developed for the grit chamber scraper, the signals from the transducers and the weather information are evaluated in such a way that the scraping cycle takes place according to the amount of grit in the channel. Unnecessary operating times during low sand accumulation, for example in dry weather, can thus be minimised considerably.
The sensors on the pressure line can be used to determine whether and how much sand is being pumped. The switch-on time of the pump and the pause time of the scraper are adjusted accordingly. If there is little or no sand accumulation, the break time is extended to a maximum of once per day. In the case of heavy sand deposits, for example, the scraper and pump are controlled (short stop in areas with maximum turbidity) so that the sand channel is largely emptied after each scraper interval. The standard programme can be modified for each installation according to the specific conditions of a grit chamber.
The Katronic flowmeters installed on the pressure line also fulfil a second purpose on wastewater treatment plants: monitoring the flow rate. As soon as the flow rate permanently falls below an adjustable limit value (wear on the impeller/clogging), a visual warning is given. With the use of this control optimisation developed by the Technisches Büro Holger Pinta, all processes around grit chambers in wastewater treatment plants become clear. Plant operators can not only control the pump and scraper more efficiently, but they can have a continuous view of the process at any time if there is a risk of wear of the pumps and/or the impeller or if too much energy is being used.
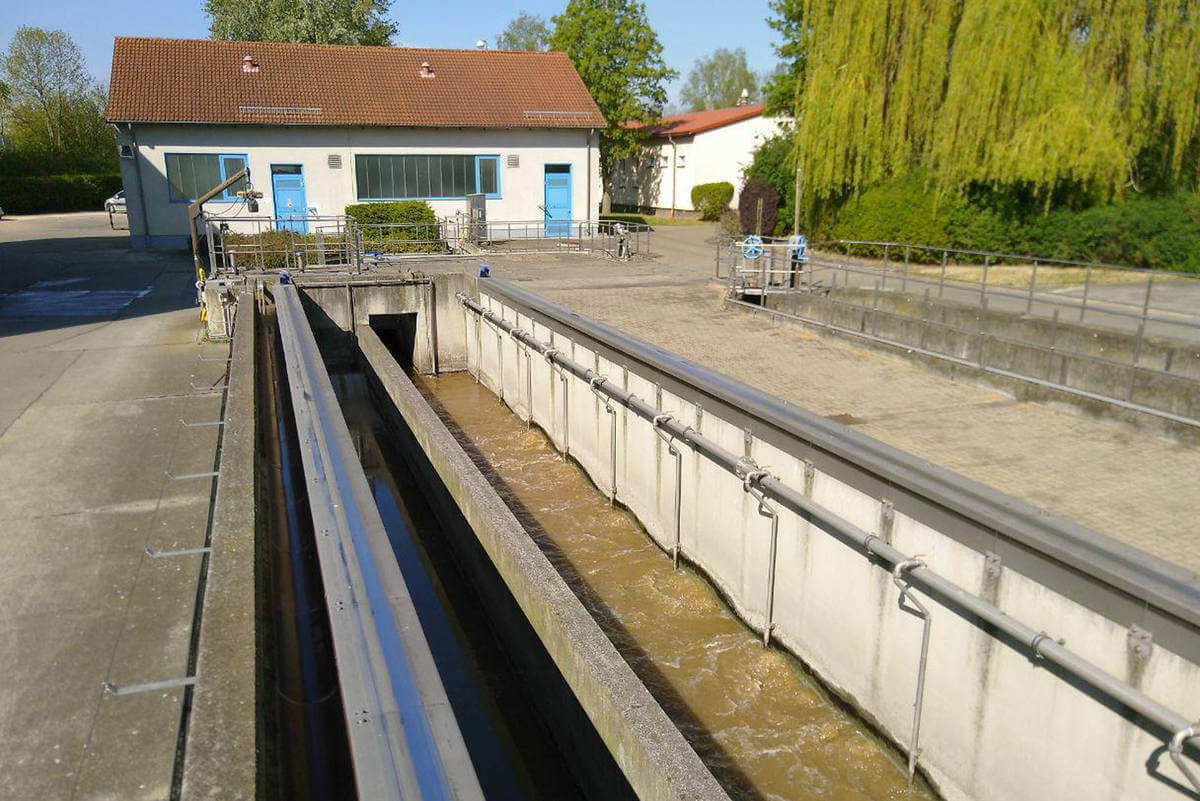
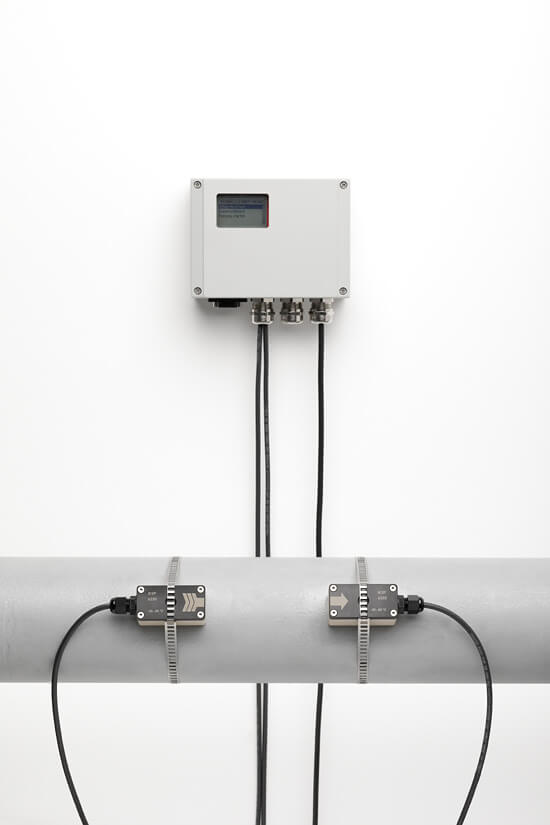